Understanding the Essentials and Applications of Plastic Extrusion in Modern Manufacturing
In the world of modern production, the technique of plastic extrusion plays an instrumental role - plastic extrusion. This intricate process, including the melting and shaping of plastic through specialized passes away, is leveraged across numerous markets for the creation of varied products. From auto parts to durable goods packaging, the applications are substantial, and the possibility for sustainability is similarly impressive. Unraveling the fundamentals of this procedure discloses truth flexibility and possibility of plastic extrusion.
The Principles of Plastic Extrusion Process
While it might appear complex, the basics of the plastic extrusion process are based on fairly simple principles. It is a manufacturing process wherein plastic is thawed and after that formed into a continuous profile with a die. The plastic extrusion procedure is extensively made use of in numerous industries due to its performance, convenience, and cost-effectiveness.
Different Kinds of Plastic Extrusion Techniques
Building upon the basic understanding of the plastic extrusion procedure, it is necessary to check out the various methods entailed in this production technique. In contrast, sheet extrusion creates large, flat sheets of plastic, which are commonly more processed right into items such as food packaging, shower curtains, and vehicle components. Comprehending these strategies is crucial to using plastic extrusion properly in modern-day production.

The Role of Plastic Extrusion in the Automotive Industry
An overwhelming bulk of parts in contemporary cars are products of the plastic extrusion procedure. This process has actually reinvented the automobile industry, transforming it into an extra efficient, cost-effective, and flexible production market. Plastic extrusion is mostly utilized in the production of various vehicle components such as bumpers, grills, door panels, and control panel trim. The process gives an uniform, constant output, enabling makers to produce high-volume components with great accuracy and minimal waste. The agility of the extruded plastic components adds to the total reduction in vehicle weight, enhancing site gas effectiveness. In addition, the resilience and resistance of these components to warmth, chilly, and influence enhance the long life of vehicles. Hence, plastic extrusion plays a critical role in automobile production.
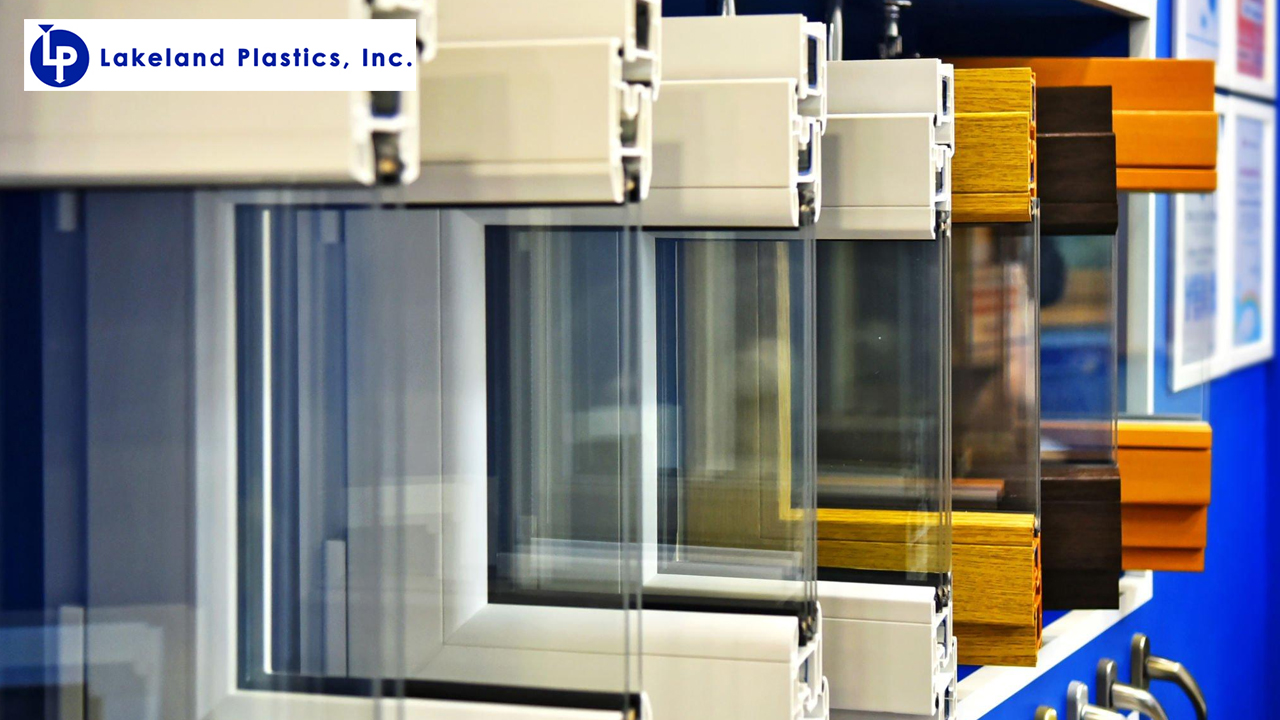
Applications of Plastic Extrusion in Consumer Item Manufacturing
Past its significant influence on the automotive market, plastic extrusion confirms equally effective in the realm of durable goods manufacturing. This procedure is crucial in creating a wide array of items, from food product packaging to house devices, toys, and even medical devices. The adaptability of plastic extrusion allows producers to develop and produce intricate forms and sizes with high precision and efficiency. Due to the recyclability of numerous plastics, squeezed out parts can be recycled, minimizing waste and expense (plastic extrusion). The flexibility, adaptability, and cost-effectiveness of plastic extrusion make it a preferred selection for numerous consumer items manufacturers, adding considerably to the market's growth and innovation. However, the environmental implications of this prevalent usage require careful consideration, a subject to be talked about better in the succeeding read here section.
Ecological Influence and Sustainability in Plastic Extrusion
The prevalent use of plastic extrusion in producing invites scrutiny of its eco-friendly effects. Efficient machinery lowers energy use, while waste administration systems reuse go to this website scrap plastic, lowering raw product needs. Despite these improvements, further advancement is needed to alleviate the environmental impact of plastic extrusion.
Conclusion
In conclusion, plastic extrusion plays an essential role in modern manufacturing, particularly in the vehicle and customer items sectors. Comprehending the essentials of this procedure is key to enhancing its applications and benefits.

The plastic extrusion process is thoroughly made use of in different markets due to its adaptability, cost-effectiveness, and effectiveness.
Building upon the standard understanding of the plastic extrusion process, it is necessary to discover the different methods entailed in this production method. plastic extrusion. In contrast, sheet extrusion creates large, flat sheets of plastic, which are generally more processed right into items such as food product packaging, shower curtains, and vehicle parts.An overwhelming bulk of parts in modern automobiles are items of the plastic extrusion procedure